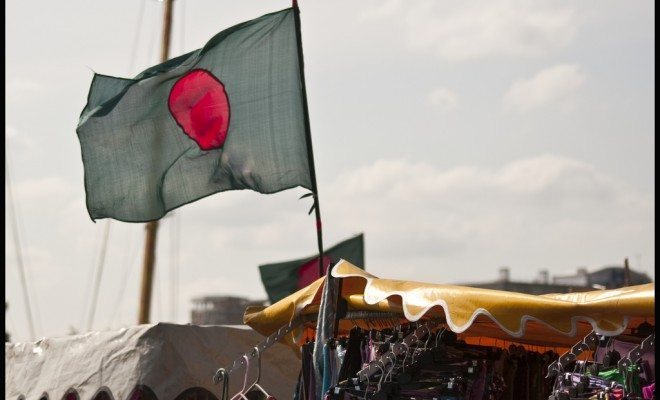
News
The U.S. Military & Bangladeshi Factories: Who’s Responsible for Safety?
The U.S. military isn’t doing enough to protect the health and safety of the people who make their clothing, according to The International Labor Rights Forum (ILRF). In the ILRF’s recent report, Dangerous Silence, the organization asserts that the U.S. Military has not properly looked into the sources of the clothing sold in their over 1,100 base stores, much of which comes from outsourced factories in Bangladesh.
According to the ILRF, the military doesn’t gather sufficient information about the safety conditions and treatment of workers in these factories, and in many cases, relies on audits by companies such as Walmart and Sears that have failed to properly protect workers in their own factories. In some cases the military exchanges were aware of safety violations but did not alert Bangladeshi authorities; for instance, the Army and Air Force Exchange failed to act when they learned that Green Fair Textiles workers were being submitted to 80-hour work weeks.
Considering the fact that it is legal for the military to use overseas suppliers, some believe that they do not need to protect the factory workers. Army and Air Force Exchange Service spokesman Judd Anstey stated that the agency abides by guidelines issued by the Department of Defense which necessitates that all local laws are followed and merchandise is not made by forced labor or children. But what about overworking those in factories that is illegal by American standards, if not locally?
The military exchanges’ failure to report and solve the problems with their clothing suppliers is all the more surprising in the wake of last years’ tragedies in Bangladesh. The Tazreen Fashions factory, which manufactured Marine Corps logo clothing, experienced a fire in which 112 workers died. In April 2013 at Rana Plaza an eight-story clothing factory collapsed, killing more than 1,134 people and leaving 200 people missing as of last December.
The U.S. military fights for freedom across the world and defends liberty at home, yet the message strikes some as hypocritical when their uniforms are made in places that condone human rights violations. Although the U.S. has no legal responsibility for the conditions in factories in other countries, government entities should not turn a blind eye to the safety and labor violations in the factories they patronize.
An interesting comparison is the nearly nonexistent criticism directed toward military exchanges with the public’s reaction to the 2012 U.S. Olympic uniform controversy; the difference is striking. Ralph Lauren received a significant amount of negative press during the London Olympics because the U.S. delegation’s uniforms were made in China rather than domestically. Perhaps the backlash to this outsourcing was due to the fact that the Olympics is a spectacle that attracts international attention, while the military exchanges lack public prominence. Nevertheless, the Ralph Lauren controversy shows how public outcry can stimulate change: in reaction to the negative press over their uniforms, Ralph Lauren made a point to use American sources and labor for the 2014 Sochi uniforms. If the military exchanges garnered the same level of attention, perhaps they would be compelled to act, too.
United States officials should take a stance against this abuse of workers and safety in outsourced factories in order to set an example for other retailers to follow when it comes to factory conditions. The ILRF’s report provides several suggestions as to how the United States military can help protect Bangladeshi workers, including requiring suppliers to comply with international labor standards, issuing mandatory repairs and inspections to ensure safety, organizing worker unions and committees, and publicly disclosing audit results. The Marine Corps appears to be taking the lead. The branch’s Trademark and Licensing Office issued a new policy mandating its retail suppliers be signatories to the Accord on Fire and Building Safety.
—

Comments